A sensor for insitu monitoring of refractory thickness
http://accl.inn.demokritos.gr/index.php/research/industrial/industrial-sensors
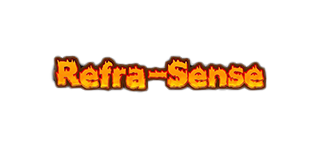
ACRONYM:
RefraSense
LEADER:
George Vekinis
START DATE:
01/09/2014
LATE DATE:
31/01/2015
FUNDING SOURCE:
ESA-TechTransfer