HYBRID ABLATIVE DEVELOPMENT FOR RE-ENTRY IN PLANETARY ATMOSPHERIC THERMAL PROTECTION
https://cordis.europa.eu/project/id/283797/reporting
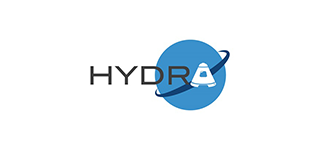
ACRONYM:
HYDRA
LEADER:
George Vekinis
START DATE:
01/02/2012
LATE DATE:
28/02/2015
FUNDING SOURCE:
FP7-Space