Computational Materials Science – Multiscale Modeling of Material Performance
Multi-scale structural modeling of composite materials and objects manufactured from them allows for investigating their thermo-mechanical performance under external loads through simulations using the finite element method (FEM). For the FEM simulations the ANSYS 19.0 Workbench is used (ANSYS Inc., Canonsburg). The models are developed on different scale levels starting from 3D models of the materials’ microstructures, the immediate contact areas of indenters during material testing up to the interaction of entire objects or structures, such as deformation and failure of ceramic vessel under mechanical loads or impact forces. In this way material tests can be simulated and interpreted, providing an estimation of effective material properties of composite materials. Furthermore, the performance and even the potential damage risk of objects or structures under thermo-mechanical loads can be predicted.
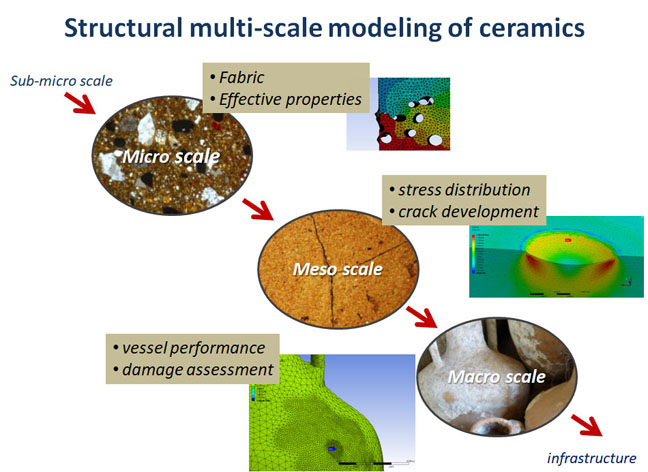
Current research concerns for example the investigation of apparent elasto-plastic deformation of ceramics under compression due to sub-surface micro-damages, the consideration of which provides appropriate simulations of experimentally determined load displacement curves recorded in material tests. For the generation of realistic 3D models of ceramics’ microstructures a collaboration with external laboratories has been initialized, concerning the examination of ceramic fragments with micro computer tomography (μCT). In view of macro-scale simulations a case study of the development of amphora design during the Hellenistic Period has been finalized taking into account their simulated packaging during transport in cargo ships and the assumed mechanical loads, to which they were exposed during transport.
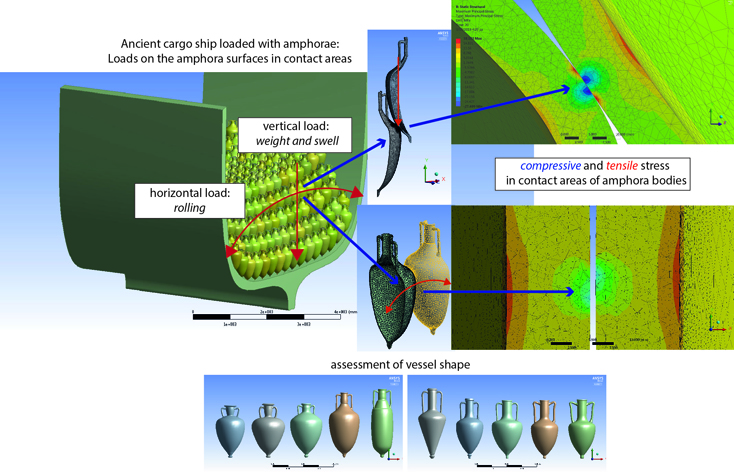
Modeling of vertical and horizontal loads on ceramic vessels stored in the hold of a cargo vessel during marine transport
FEM can be combined also with computational fluid dynamics (CFD) in order to simulate for example the heat transfer by thermal convection between solid surfaces and liquids or gases. A possible application concerns the assessment of the heating efficiency in furnace or kiln structures.
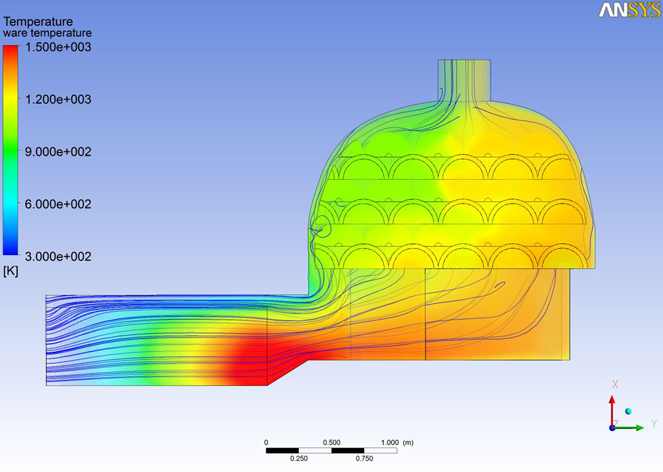
Model of the temperature distribution in a two-chamber updraft ceramic kiln
Publications
Hein, A., Kilikoglou, V., Modeling of thermal properties of ancient metallurgical ceramics, Journal of the American Ceramic Society 90, 3 (2007) 878-884. DOI: 10.1111/j.1551-2916.2006.01466.x
Hein, A., Kilikoglou, V., Breaking Pots – Simulating design failures of transport amphorae by using the finite element method (FEM), in: Papadopoulos, C., Paliou, E., Chrysanthi, A., Kotoula, E., and Sarris, A. (eds.) Proceedings of the 1st Conference on Computer Applications and Quantitative Methods in Archaeology Greek Chapter (CAA-GR) Rethymno (2015) 187-190.
Hein, A., Müller, N.S., Kilikoglou, V., In and Out: CFD modeling of the temperature distribution inside an ancient updraft kiln, in G. Vavouranakis, M. Katsianis, Y. Papadatos, M. Mouliou and P. Petridis (eds.) Digital pasts for the present - Proceedings 2nd Conference on Computer Applications and Quantitative Methods in Archaeology Greek Chapter (CAA-GR), Athens (2017) 99-104.
Hein, A., Kilikoglou, V., Modeling of the microstructure of ancient functional ceramics and assessment of their performance, Procedia Structural Integrity (2018) 219-226. DOI: 10.1016/j.prostr.2018.09.031
Hein, A., Kilikoglou, V., Digital modeling of function and performance of transport amphorae, International Journal of Ceramic Engineering & Science 2 (2020) 187–200. DOI: 10.1002/ces2.10056
Hein, A., Vekinis, G., Kilikoglou, V., Modeling of biaxial flexure tests of transport amphorae with the finite element method: Fracture Strength, Deformation and Stress Distribution, forthcoming.
Kilikoglou, V., Vekinis, G., Failure prediction and function determination of archaeological pottery by finite element analysis. Journal of Archaeological Science 29 (2002) 1317-1325. DOI: 10.1006/jasc.2001.0775