Applications
Crack detection using magnetooptic sensors
The detection of the stray magnetic field created when cracks exist in a magnetized ferromagnetic specimen, is the basic physical principle for several non-destructive methods. The most popular method of this category is the detection of cracks using magnetic particles. In addition, GMR and Hall sensors are also used. The aim of this work, is to study and develop the methodology of nondestructive evaluation of cracks created on the surface of rails, due to rolling contact fatigue (RCF). The magnetooptical phenomenon can be described phenomenologically by an electrical permittivity tensor which depends on the external magnetic field..
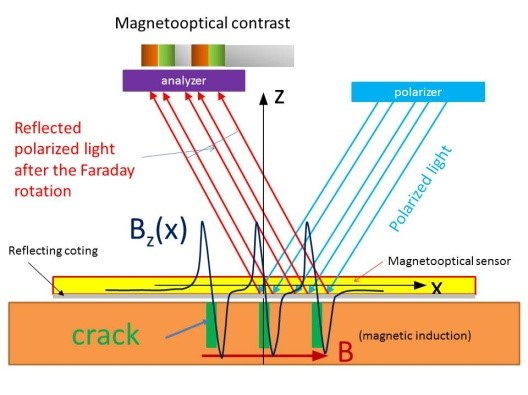
The magnetization of a material causes a secondary motion of the electrons u=-M x E (u the electron velocity, M is the magnetization of the material, and E the electric field of the incident electromagnetic wave) which in turn generates electromagnetic waves with rotated polarization plane. The material relation between the electrical displacement and the electric field will have the form D=ε(Ε+iQvM x E) where QV is the Voight constant. In a magnetooptical sensor, rotation of the polarization plane, of the reflected (Kerr effect) or of the transmitted (Faraday effect) light, could occur, respectively, depending on the magnetization of the sensor. The two phenomena are described by the general term magnetic circular dichroism (circular magnetic birefringence). Fig. 1 shows schematically how the magnetooptical contrast is generated above a magnetized specimen with cracks. Linear polarized light when passing through a transparent magnetooptical specimen, is subject to rotation of the polarization plane which depends on the direction of the magnetization. The cracks on the surface of a magnetized specimen produce stray magnetic field with different direction, on the right and the left of the crack. This effect has as consequence the opposite magnetization of the sensor, near the crack. This alternative magnetization causes different rotation of the incident light, which produces the magnetooptical contrast when it passing though the analyzer. The magnetooptical contrast is directly related with the geometrical characteristics of the cracks. In our study we used as magnetooptical sensor a thin film of the mixed garnet Y3-xBixFe5O12. This compound is a ferrimagnetic material (ferromagnetic garnet) which in non-magnetized state displays stripe-type magnetic domains, with a characteristic size of a few micrometers (see fig. 2).
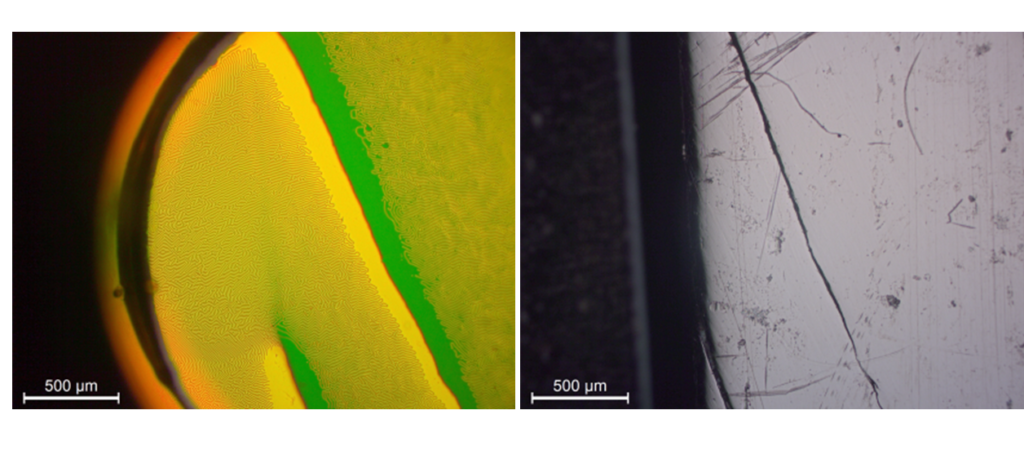
Figure 2 illustrates the generated magneto optical contrast when a magnetooptical sensor is placed above a magnetized material surface with two breaks.
Magnetic field mapping in plastically deformed soft magnetic materials
Soft magnetic materials are important components of electrical to mechanical energy conversion devices. Classic examples are electric motors and generators. The rapid increase in the use of electric cars, however, and the huge prospects in this area, make the study of magnetic losses in magnetic steels an important issue. Magnetic steels of electric motors are mainly Fe-Si alloys with or without orientation of their crystallites (texture). The most important cause of energy loss in these magnetic materials is the magnetic field lag due to the presence of crystalline boundaries, and residual mechanical stresses/stains. In this research project an attempt is made, to relate magnetic field in the surface of the magnetic steel (produced by rolling), with the remaining mechanical stresses/stains.
In the experiments we perform, we record the horizontal (parallel to the sheet) and the vertical component of the magnetic field on the outer surface of the specimens. The sheets are produced by cold rolling. The horizontal component of the magnetic field was measured with a GMR sensor, and the vertical component with a Hall sensor. The measurements were made by moving the sensor above the test piece using xy-stage (see Fig 3).
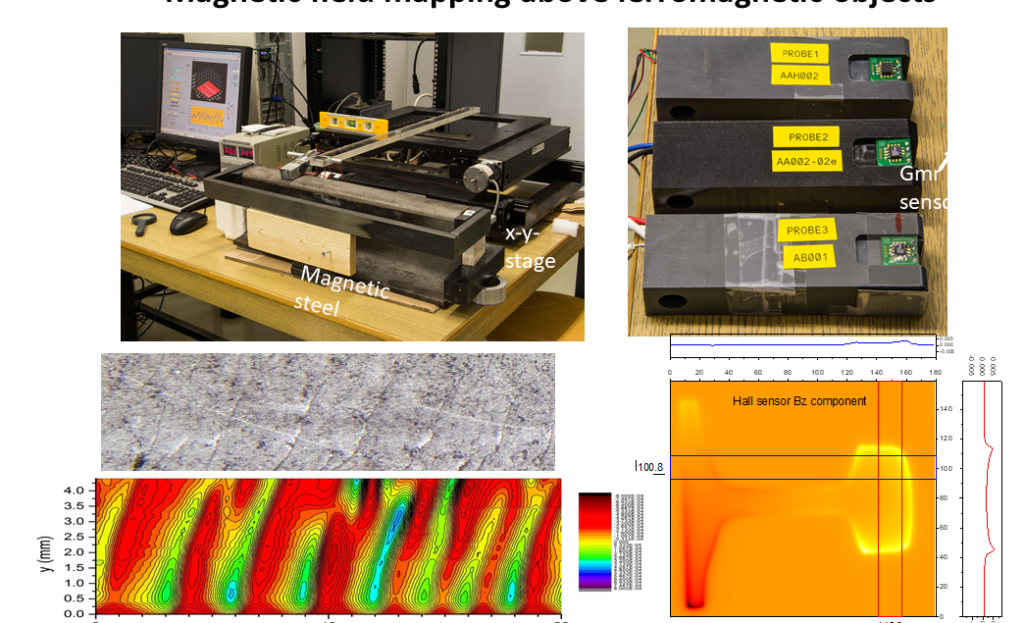
Representative results of our measurements are shown in Figure 4
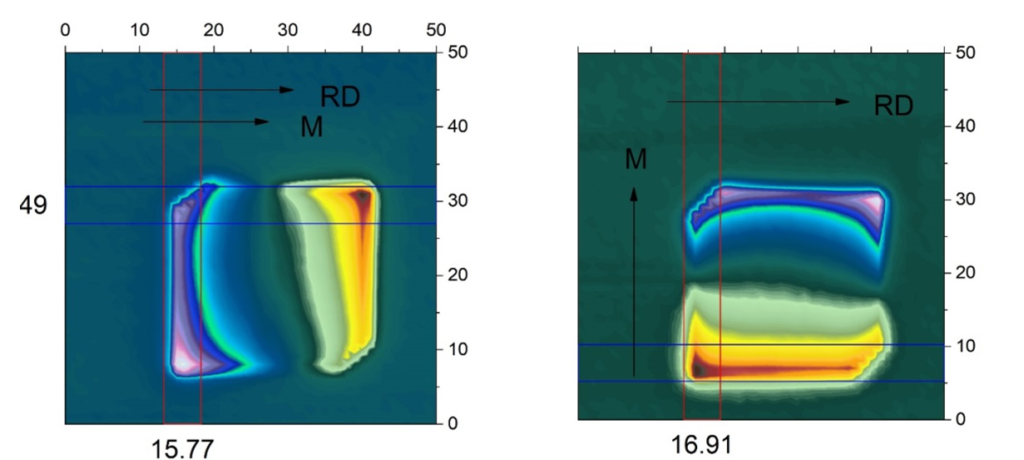